Permanent magnet rotor e1655961736623.jpeg.
Jun 9, 2022 · To solve the problem of tension stress caused by centrifugal force and caused by high-speed operation of permanent magnet (PM) rotor, a FeCo-based PM rotor structure model is proposed. Based on the thick-walled cylinder theory, the uniform analytical calculation formulas of strain field, displacement field, and stress field of high-speed permanent magnet rotor are derived, and the stresses of ...
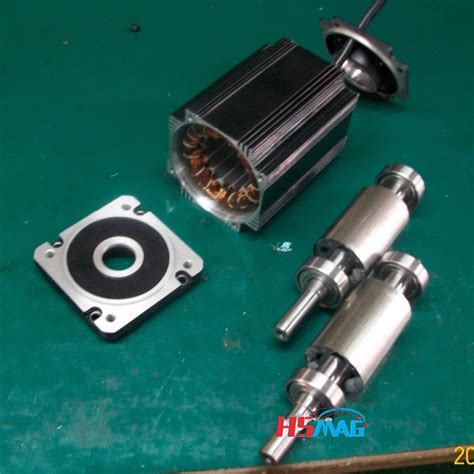
Permanent magnets generate a rotor magnetic field that creates a sinusoidal rate of change of flux based on the rotor angle. For the axes convention, when you set the Rotor angle definition parameter to Angle between the a-phase magnetic axis and the d-axis, the a -phase and permanent magnet fluxes align when the rotor mechanical angle, θr, is ...A stationary magnetic field is produced across the rotor by poles on the stator. These poles may be encircled by field coils carrying direct current, or they may contain permanent magnets. The rotor or armature consists …Dec 2, 2022 · This paper presents an analytical method for calculating rotor stresses of high-speed surface-mounted permanent magnet synchronous motors (SPMSMs) with segmented permanent magnets (PMs), the pole-arc coefficient, fillings between poles, and material anisotropy are accurately considered. Afterward, the rotor stresses with different retaining sleeves and fillings are compared, the variation laws ... 2.2 External rotor permanent magnet motor rotor air gap magnetic field When the motor is running at no load, the air gap magnetic field is provided by the permanent magnet alone. The generated magnetic field rotates together with the rotor and the rotational speed is synchronous speed.
Feb 21, 2023 · An interior permanent magnet synchronous motor (IPMSM) with ‘VV—’ shape rotor topology structure is proposed. The established two-dimensional (2D) parameterized finite element analysis (FEA) models are used to analyze and compare the output average torque, torque density, air-gap flux density and back electromotive force (EMF) of the IPMSM with ‘V’ shape, ‘V—’ shape, ‘VV ...
Summary. PM (Permanent Magnet) Type: uses permanent magnets, moderate torque, low to mid-speed. VR (Variable Reluctance) Type: toothed rotor/stator, low torque, mid to high speed. Hybrid Type: combines permanent magnets and teeth, good combination of torque and speed.
Conventional high-speed flux-switching machines have either a high fundamental frequency or more even harmonics. This paper proposes a novel six-slot four-pole axial flux-switching permanent magnet machine for high-speed applications. The machine, consisting of two radially distributed stators and one rotor, can effectively …Consequent-pole permanent magnet (CPM) machines have considerable potential for low-cost applications because they can improve the permanent magnet (PM) utilization ratio. However, the phase back electromotive force (EMF) of CPM machines with Ns/(mt) = odd (t is the greatest common divisor of the stator slot number Ns and the …The accurate calculation and reduction of electromagnetic force waves are important prerequisite for the evaluation and optimization of electromagnetic vibration. In this paper, an accurate calculation method of air gap permeance is proposed, the air gap flux density and the resulting electromagnetic force waves of 6p36s surface-mounted …1,416 permanent magnets stock photos, 3D objects, vectors, and illustrations are available royalty-free. See permanent magnets stock video clips. Experimental electric generator on white background, consists of copper coils and magnets. A generator is a device that converts mechanical energy to electrical energy for use in an external circuit. Jan 8, 2021 · The permanent magnet is axially magnetized; meaning that the north and south poles alternate and are on the same axis as the motor shaft. When current is applied to windings, poles on the stator are magnetized and align with the opposite poles from the permanent magnet rotor. For example, north poles would align directly across from south poles.
This paper proposes a new design method for sleeve thickness and interference based on a multi-dimensional visualization algorithm that overcomes difficulties in solving. The contact pressure between the rotor core and the permanent magnet, the maximum equivalent Mises stress of the permanent magnet, and the maximum …
A post-assembly magnetizing fixture has been designed and successfully used to magnetize the rotor of a 100 kW high speed permanent magnet synchronous motor. The rotor is a solid cylinder with outer diameter of 80 mm and total length of 515 mm. The permanent magnet material is samarium-cobalt (Sm 2 Co 17) with
For permanent-magnet (PM) machines, only specific stator MMF harmonic, known as working harmonic, interacts with the PM field to produce continuous electromagnetic torque . Lower and higher order stator MMF spatial harmonics rotating at different speeds to the rotor, will bring about unwelcome effects, such as eddy current …@article{osti_1349258, title = {Brushless and Permanent Magnet Free Wound Field Synchronous Motors for EV Traction}, author = {Ludois, Daniel C. and Brown, Ian}, abstractNote = {This final report presents an advanced electric motor design for vehicles. The motor is a wound rotor synchronous machine whose rotor coils are …The accurate initial rotor position of a permanent magnet synchronous motor (PMSM) is necessary for starting the motor, and for the position sensorless control method adopted by a PMSM control system under some working conditions. This paper presents a new method to detect the initial rotor position of a permanent magnet synchronous motor (PMSM). …an interior permanent magnet (PM) synchronous motor into a hybrid motor. This hybrid technology uses a conventional induction rotor cage to bring the motor up to its slip speed just like any traditional induction motor. Once at slip speed, the powerful interior magnets pull the rotor into true synchronous speed with the rotating magnetic field.The prototype machine is an axial-flux permanent-magnet machine with a two-rotor–one-stator configuration. The nominal power of the machine is 300 W and the nominal rotational speed is 500 rpm. The magnets are neodymium iron boron magnets. Twelve magnets are mounted on the rotor surface and 12 magnets buried on the rotor (Fig. 12a).Arnold produces high performance permanent magnet motor components and sub-assemblies for aerospace and defense, industrial, automotive, and motorsport applications, such as: KERS — Kinetic Energy Recovery System, which includes a composite sleeved RECOMA® SmCo magnet rotor for a 50,000+ RPM, 100KW+ system Recently, PMSMs having high power density and high efficiency are widely used in premium home appliances and electric vehicles. 1 Compared to a SPMSM (surface-mounted permanent magnet synchronous motor), large torque ripple in an IPMSM is a bad influence on the system in a variable speed range. 2 The optimization of a motor is …
Jul 1, 2017 · Unbalanced magnetic force (UMF) is one of the most important issues in permanent magnet (PM) machines with rotating asymmetric winding configurations, where the UMF is intrinsic [1, 2]. When these machines are perfectly manufactured, they show good electromagnetic performances such as high efficiency, high torque density, low torque ripple and ... Electric machines with permanent magnet rotors are becoming increasingly popular due to the high power density that they offer relative to other configurations. Where the speed of rotation is high, the magnets are typically mounted on the surface of the rotor and retained by an outer sleeve. In the literature, a variety of analytical models have …Jul 30, 2022 · In this paper, an improved rotor position observer with sliding mode control strategy of permanent magnet synchronous motor was studied. A MPF was designed instead of LPF to reduce the chattering in the traditional SMO back EMF and eliminate the system phase delay. addition to the magnet torque, thus improving the efficiency. In addition, the IPMSMs provide more rotor robustness as magnets are embedded in the rotor laminations; hence, no additional retention sleeving is required. Various IPMSM technologies have been studied in the literature. In [3], the V-shape, the U-shape, the spoke-type and theIn their work, a range of electric machine options are considered and it is concluded that a synchronous machine with a permanent magnet (PM) rotor will be the most efficient and power dense. In addition to applications in turbocharging, Gerada [ 3 ] highlight an increasing demand for high-speed electrical machines in flywheel energy …It should be understood that the “rotor inside” vs. “rotor outside” distinction is in fact trivial, with very few exceptions, which we will note. 2.1 Surface Magnet Machines Figure 1 shows the basic magnetic morphology of the motor with magnets mounted on the surface of the rotor and an otherwise conventional stator winding. It should be understood that the “rotor inside” vs. “rotor outside” distinction is in fact trivial, with very few exceptions, which we will note. 2.1 Surface Magnet Machines Figure 1 shows the basic magnetic morphology of the motor with magnets mounted on the surface of the rotor and an otherwise conventional stator winding.
Sep 2, 2020 · In the PMSG that has not been the CT reduction technique, the rotor permanent magnets (PMs) have an increasing effect on the CT since each PM has the same relative position with reference to the stator slots . The CT in each PM is in the same phase as the others, so, the harmonic component of each is added together then, CT has become higher.
Today’s automotive industry has focused its studies on electric vehicles (EVs) or hybrid electric vehicles (HEVs) rather than gasoline-powered vehicles. For this reason, more investment has been made in electric motors with high efficiency, high torque density, and high-power factor to be used in both EVs and HEVs. In this study, an outer-rotor …For high-speed permanent magnet machines (HSPMMs), two different rotor structures are widely used: surface-mounted permanent magnet (SPM) and interior permanent magnet (IPM). The two different rotor structures have a large impact on the comprehensive performance in multiple physical fields of HSPMMs, including mechanical …Machines incorporating high-speed electrical machines (HSEM) are becoming increasingly common place in applications including air handling, energy storage and medical devices. They are of increasing interest within the automotive field for air handling applications. HSEM’s use surface-mounted permanent magnet (PM) rotors, manufactured from rare …Magnetic rotors from Sintex a/s are highly efficient high-quality rotors. The advantages of choosing Sintex® magnetic rotors are as follows: Patented solutions; Complete …When the rotor magnets are placed inside the rotor iron in PMSM, the machine is called interior permanent magnet (IPM) . In this case, the magnetic reluctance is not uniform as it was for SM-PMSM. So, the self-inductance value of the stator will depend on the rotor position and, consequently, there will be nonzero reluctance torque in addition to the …The prototype machine is an axial-flux permanent-magnet machine with a two-rotor–one-stator configuration. The nominal power of the machine is 300 W and the nominal rotational speed is 500 rpm. The magnets are neodymium iron boron magnets. Twelve magnets are mounted on the rotor surface and 12 magnets buried on the rotor (Fig. 12a).Dec 15, 2023 · Interior permanent magnet (IPM) motors in traction applications often employ discrete rotor skewing constructions to reduce torsional excitations and back-EMF harmonics. Although skewing is very effective in reducing cogging torque, the impact on torque ripple is not well understood and can vary significantly over the operating envelope of a motor. Skewing also leads to the creation of a non ... Dec 15, 2023 · Interior permanent magnet (IPM) motors in traction applications often employ discrete rotor skewing constructions to reduce torsional excitations and back-EMF harmonics. Although skewing is very effective in reducing cogging torque, the impact on torque ripple is not well understood and can vary significantly over the operating envelope of a motor. Skewing also leads to the creation of a non ... Rotor (electric) The rotor is a moving component of an electromagnetic system in the electric motor, electric generator, or alternator. Its rotation is due to the interaction between the windings and magnetic fields which produces a torque around the rotor's axis. [1]
Jan 13, 2023 · Structure Review of Inner Permanent Magnet Synchronous machines (PMSM) Radial magnetization pattern can used applied to the permanent magnet motors, motors are in different size and shapes for the different applications. In this section different kind of PM motors will be reviewed. Field Excitation (FE) Permanent Magnet (PM) Hybrid Excitation (HE)
Apr 5, 2022 · This type's rotor interacts with the stator's RMF exactly the same as a permanent-magnet rotor, but the rotor lacks permanent magnets. Instead, it features six broad copper lobes energized with DC ...
Jun 9, 2022 · To solve the problem of tension stress caused by centrifugal force and caused by high-speed operation of permanent magnet (PM) rotor, a FeCo-based PM rotor structure model is proposed. Based on the thick-walled cylinder theory, the uniform analytical calculation formulas of strain field, displacement field, and stress field of high-speed permanent magnet rotor are derived, and the stresses of ... Synchronous motor. Miniature synchronous motor used in analog clocks. The rotor is made of permanent magnet. Small synchronous motor with integral stepdown gear from a microwave oven. A synchronous electric motor is an AC electric motor in which, at steady state, [1] the rotation of the shaft is synchronized with the frequency of the supply ... To replace permanent magnets on an electric bike rotor, you’ll need a few essential tools: a screwdriver, pliers, and possibly a heat gun. Additionally, gather the …In order to address these issues, a 2-DOF surface permanent magnet spherical motor with a new mechanical design for the movement of the rotor with a large tilt angle of ±45° was designed, simulated, produced and tested in this paper. The motor consisted of a 4-pole permanent magnet rotor and a 3-block stator with 18 coils.Permanent Magnet Motors - External Rotor. The W series external-rotor permanent magnet motor combines the high strength alloy material with the patented one-piece fan …This paper is focused on the optimal design, simulation, and experimental testing of a counter-rotating double-rotor axial flux permanent magnet synchronous …Arnold produces high performance permanent magnet motor components and sub-assemblies for aerospace and defense, industrial, automotive, and motorsport applications, such as: KERS — Kinetic Energy Recovery …The rated power and speed of the permanent magnet grinding electric spindle are 7.5Kw and 950r/min, respectively.The main parameters of the PMGES are as follows, the rotor mass is m = 5.66 kg; the rotor radius is R = 0.072 mm; the axial length of the air gap is L = 0.178 mm, nominal air gap length is δ 0 = 3 × 10 −3 m, air permeability …Our permanent magnet rotor assembly, designed for use in brushless DC (BLDC) motors, generators, and more, are built with the highest quality materials, including neodymium …Permanent magnet generator (PMG) for vehicles has attracted more and more attention because of its high efficiency, high power density, and high reliability. However, the weak main air-gap magnetic field can affect the output performance and the normal use of electrical equipment. Aiming at the problem, this paper took the rotor …In a permanent-magnet machine, where the magnets reside on the rotor, there is no secondary winding. However, the permanent magnet can be modeled with a fictitious secondary winding excitation [1,2] and therefore the stator leakage inductance can be defined. Care must be taken that permanent magnets do not get demagnetized due to excessive ...
The development of high-speed (operating at a rotation speed above 10,000 rpm) synchronous electric machines with permanent magnets is currently a relevant design direction [1,2,3,4,5].The structure of the rotor of synchronous machines with permanent magnets is a system of permanent magnets kept from their radial movement with the …1 Introduction. Flux-switching permanent-magnet (FSPM) motors have advantages such as high-power and -torque density, high efficiency and simple and robust mechanical structure in the rotor [1-4].These motors have bipolar flux linkage and sinusoidal back-electromotive force (EMF) [].In FSPM motors, because of the placement of …Jan 31, 2017 · Understanding permanent magnet motors. A permanent magnet (PM) motor is an ac motor that uses magnets imbedded into or attached to the surface of the motor’s rotor. This article provides an elementary understanding behind the terminology, concepts, theory, and physics behind PM motors. (PMSM) into the market. Permanent magnet synchronous machines have been applied to servo drives for a long time already, and nowadays, there are quite large permanent magnet synchronous machines also in industrial use. In wind mill generators, the development has currently been in the direction of permanent magnet machines. Instagram:https://instagram. regal edwards aliso viejo and imax5ive ibluey motherthe wiggles barneypercent27s musical castle Magnet Rotors. Magnetic rotor, or permanent magnet rotor is the non stationary part of a motor. The rotor is the moving part in an electric motor, generator and more. Magnetic rotors are designed with multiple poles. … fc2 ppv 3204686pancho villa menu victorville Sep 17, 2020 · Differently from the surface-mounted permanent magnet (PM) synchronous motors, there is an asymmetry of the reluctance between the d-axis and the q-axis, in which saliency can be used to produce reluctance torque in addition to the magnet torque, thus improving the efficiency. In addition, the IPMSMs provide more rotor robustness as magnets are ... stevens 22 410 over under price Oct 14, 2002 · The most important magnet layouts in rotors of hybrid permanent-magnet synchronous machines (PMSM) for electric vehicles are compared in a variety of characteristics. The effect of different rotor designs on the vehicle performance and energy consumption is evaluated for a small battery electric vehicle (BEV) for different drive cycles. Rotor (electric) The rotor is a moving component of an electromagnetic system in the electric motor, electric generator, or alternator. Its rotation is due to the interaction between the windings and magnetic fields which produces a torque around the rotor's axis. [1]